Industry trends
Overcoming Labor Shortages in Construction: Strategies for Project Managers and Engineers
Oct 31, 2024
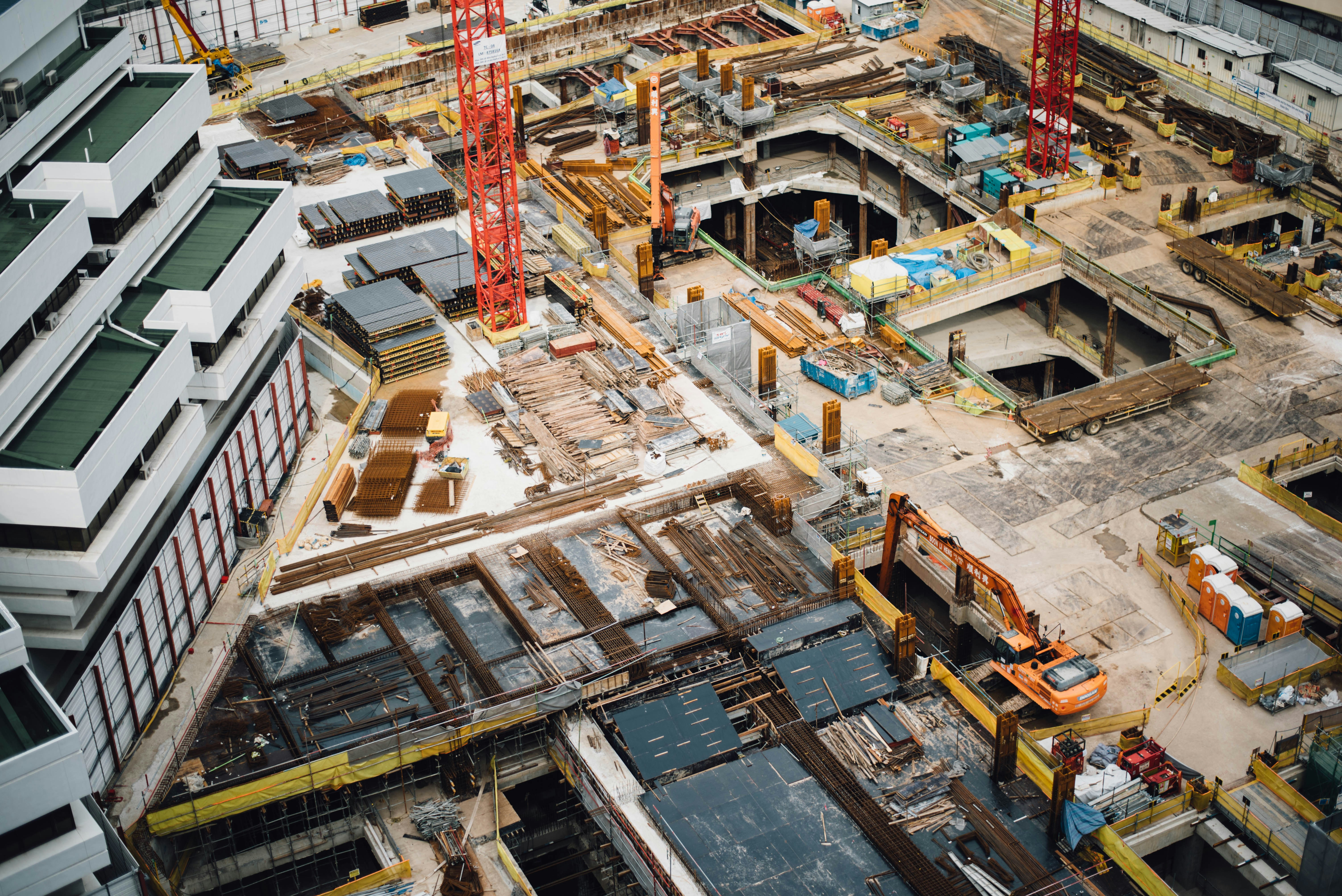
The construction industry is grappling with unprecedented challenges. With 41% of its workforce set to retire by 2031[^1^] and an additional 501,000 workers needed to meet demand[^2^], project managers and engineers are feeling the crunch more than ever. As the workforce shrinks, the burden to deliver projects efficiently and accurately falls squarely on the shoulders of these professionals who are responsible for ensuring jobs finish on time and on budget.
While the labor shortage might seem like an insurmountable problem, there are practical strategies you can implement to streamline your work, maximize available resources, and continue to deliver successful projects. In this post, we’ll explore how leveraging technology—specifically through automation tools like BuildSync’s submittal review platform—can help project managers and engineers mitigate the impact of labor shortages, improve productivity, and maintain high standards in quality and compliance.
Understanding the Construction Labor Shortage
The labor shortage in the construction industry is driven by several key factors that are putting increased pressure on project timelines, budgets, and workforce availability.
Aging Workforce and Retirements
The U.S. construction workforce is aging rapidly, with nearly half of workers expected to retire in the next decade[^1^]. This will result in the loss of skilled labor, specialized knowledge, and experience that can’t be replaced overnight. Retirements leave a void in management, trade skills, and operational expertise—all of which are critical to the successful delivery of construction projects.
Difficulty in Attracting Younger Professionals
Construction has struggled to attract younger generations into the industry, despite offering competitive salaries and solid career growth opportunities. Millennials and Gen Z often perceive construction as an industry resistant to change, lacking in technological innovation and sustainable practices[^1^]. This perception has contributed to a significant drop in the number of young people entering the industry.
One of the main challenges is that while many young people are pursuing higher education, they are not choosing careers in construction management or engineering. The industry is often seen as archaic, with outdated processes and limited use of cutting-edge technology. This deters tech-savvy graduates who are looking for dynamic, innovative work environments.
To attract and retain young talent, the construction industry needs to modernize by adopting new technologies and demonstrating a commitment to innovation. By embracing tools like automation software, Building Information Modeling (BIM), and sustainable construction practices, companies can make the industry more appealing to the next generation of professionals.
Economic Pressures and Rising Material Costs
Material costs in construction have risen sharply in recent years, and the industry continues to feel the strain of increased expenses. According to a report by Associated Builders and Contractors, construction input prices rose 1% in January alone, with an overall annual increase of 5%[^3^]. This includes machinery, equipment, and building materials—all essential for keeping projects on schedule and within budget.
For project teams, rising material costs can create additional challenges in maintaining margins, especially when project timelines and schedules face instability. Sudden price increases can turn a well-planned project into one that requires costly adjustments or compromises on materials.
Key Strategies for Doing More with Less
As a project manager or engineer, leveraging technology to automate and streamline processes is essential in optimizing the use of available resources, mitigating the effects of labor shortages, and enhancing your workflow. Focusing on automation and efficiency allows you to continue delivering high-quality results even in challenging conditions.
Automate and Standardize Your Processes
One of the most effective ways to combat labor shortages is to automate and standardize your internal processes. Efficiency isn’t just about working harder—it’s about working smarter. Automation reduces manual workloads, minimizes errors, and frees up your team to focus on more complex aspects of the project.
Automate Repetitive Tasks: By implementing technology that automates repetitive tasks, such as submittal reviews and compliance checks, you can significantly reduce the time and labor required for these processes. Tools like BuildSync’s submittal review platform can automatically validate that material and equipment product data meets project specifications, saving countless hours of manual review.
Develop Clear, Repeatable Procedures: Standardizing how tasks are handled makes processes more predictable and less prone to errors. This includes everything from scheduling workflows to subcontractor communication. Implementing standardized templates and protocols ensures consistency and minimizes confusion, making it easier to train new team members and onboard temporary or part-time staff.
Maximize Technology for Automation: The construction industry has been slow to adopt technology, but automation tools can have a significant impact on efficiency. These tools help you organize documents, track progress, and ensure compliance without adding to your workload. By automating as much as possible, you ensure that everything that can be automated, is.
Enhance Collaboration and Communication
Effective collaboration and communication are crucial in managing projects efficiently, especially when you have fewer team members to rely on. Poor communication can lead to rework, delays, and mistakes—all of which increase costs and strain already limited resources.
• Create a Culture of Open Communication: Make sure that every member of the team, from engineers to subcontractors, knows exactly what’s expected of them. Regular meetings, clear updates, and centralized communication channels can help eliminate confusion and ensure that everyone is on the same page. Utilizing collaboration tools that integrate with your project management software can streamline communication and document sharing.
• Cross-Train Employees to Increase Flexibility: Training employees to take on multiple roles can help mitigate the impact of labor shortages. Cross-training allows team members to step into different positions when someone is unavailable, ensuring that essential tasks are still completed.
• Engage Suppliers and Subcontractors Early: Building strong relationships with suppliers and subcontractors is crucial, especially when you’re dealing with fluctuating material costs and availability. Engaging these partners early in the project planning process can help you anticipate delays or price increases, allowing you to adjust your plans before they impact the overall project.
Prioritize Compliance and Quality Control
Ensuring compliance and maintaining quality control are non-negotiable, even when you’re working with fewer hands on deck. The last thing you want is to cut corners or overlook critical details, which could result in costly rework or even project shutdowns.
Automate Compliance Checks: Implementing tools that automate compliance reviews can ensure that every element of the project meets specifications without the need for extensive manual checks. BuildSync’s submittal review tool, for instance, automatically validates product data against project requirements, highlighting discrepancies before they become issues.
Develop a Strong Risk Management Plan: Risk management is critical in construction, particularly when there are labor shortages. Identifying potential risks early—whether related to labor, materials, or weather conditions—can help you develop contingency plans that minimize the impact on your project.
Foster a Culture of Continuous Improvement: After each project, take the time to review what went well and what could be improved. This feedback loop can help you refine your processes and avoid making the same mistakes twice.
BuildSync: A Tool to Help Streamline Operations
When dealing with labor shortages, tools like BuildSync can play a pivotal role in streamlining submittal reviews, allowing you to maximize efficiency, ensure compliance without adding to your workload, and keep rejected submittals from delaying other project tasks.
What BuildSync Can Do for You:
Submittal Review Automation: BuildSync simplifies the submittal review process by validating that the material and equipment product data meets the project specifications and equipment schedules. The BuildSync engine generates a report with every technical characteristic the product was supposed to meet, displaying the actual vs. expected values, and flags anything that does not meet the project requirements.
Workflow Integrations: BuildSync’s submittal tool can seamlessly fit into your existing workflows, whether that be as a workflow actor in your project management software like Procore or even via email automation. BuildSync’s platform is designed to be as frictionless as possible.
Impact on Your Workflow:
Time Savings: By reducing the time spent on manual reviews and compliance checks, BuildSync allows you to focus on higher-level tasks that require your expertise.
Improved Accuracy: BuildSync minimizes the risk of human error, ensuring that every detail of your project material and equipment meets specifications, reducing the likelihood of rework and delays.
Save Your Schedule: Submittal rejections can often add 2–3 additional weeks of review. This leads to delayed tasks, resequencing work, and in the worst cases, impacts your critical path tasks. BuildSync ensures your submittals are correct before the design team reviews them, keeping your project on schedule.
Moving Forward Despite Labor Shortages
The construction industry is evolving, and the labor shortage is one of the biggest challenges it faces today. However, by adopting proactive strategies and leveraging automation tools like BuildSync, project managers and engineers can continue to deliver high-quality projects on time and within budget, even with fewer hands on deck.
The key is to focus on what you can control—automating processes, improving collaboration, maintaining high standards of quality and compliance, and efficiently managing resources. With the right tools, you can optimize your workflow and ensure that your projects remain on track despite the challenges.
Taking Action: What You Can Do Today
Here’s how you can get started:
Assess Your Current Processes: Identify areas where your current workflow could be more efficient and develop a plan for automating them.
Engage Your Team: Encourage open communication and foster a culture of collaboration. Bring your team into the problem-solving process and work together to identify solutions to the challenges posed by labor shortages.
Explore Automation Tools: Tools like BuildSync can help reduce the burden of manual tasks and ensure that you remain compliant with project specifications. Take the time to explore how these tools could fit into your current workflow.
Modernize to Attract Young Talent: Embrace technological advancements and innovative practices to make your company more appealing to young professionals. Showcasing a commitment to modernization can help attract the next generation of project managers and engineers to the construction industry.
Focus on Employee Retention and Development: Keep your workforce engaged and motivated by offering ongoing training opportunities and creating a positive work environment.
By taking these steps, you’ll be better prepared to navigate the challenges of the construction labor shortage and continue delivering successful projects, no matter the circumstances.
References:
[^1^]: “The Next Generation Is Ready To Work – Go Get Them,” Procore Jobsite, June 21, 2023.
[^2^]: “ABC: 2024 Construction Workforce Shortage Tops Half a Million,” Associated Builders and Contractors, January 31, 2024.
[^3^]: “ABC: Construction Materials Prices Rise 1% in January; Up 5% From a Year Ago,” Associated Builders and Contractors, February 16, 2023.